10 Industrial IoT Trends Transforming Manufacturing in 2025
After spending 15 years on factory replica Rolex submariner floors across three continents, I’ve witnessed firsthand how manufacturing has evolved from clipboard-wielding supervisors to sophisticated digital environments.
Nothing has changed the game quite like Industrial IoT. Let replica watches uk me share what I’m seeing in real manufacturing environments this year—not just the flashy tech demos top uk replica watches at trade shows, but the actual implementations making a difference.
What Is Industrial IoT?
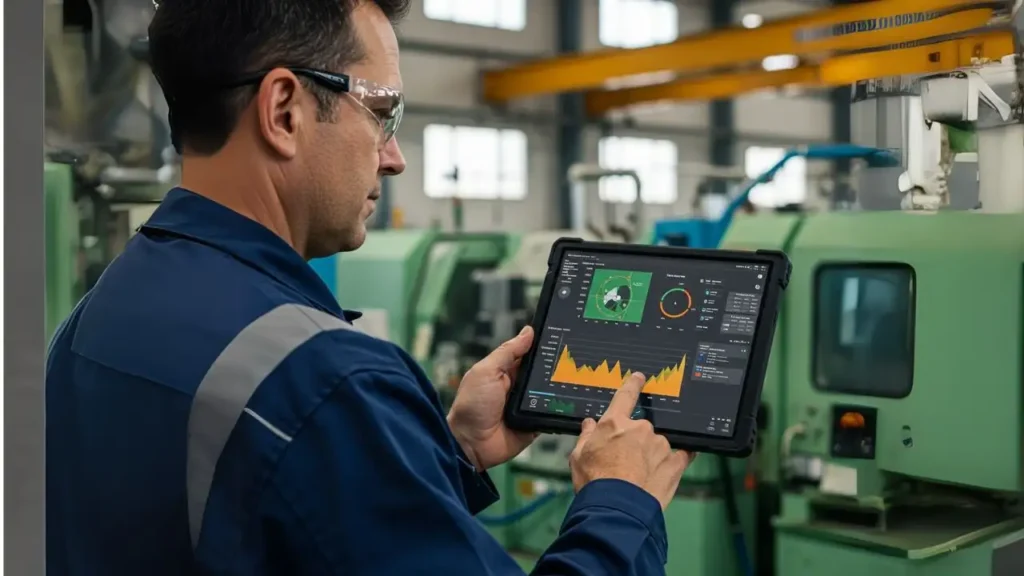
IIoT isn’t just a buzzword—though heavens know I’ve sat through enough PowerPoint presentations where it was treated as one! In simple terms, it’s connecting machines to networks so they can talk to each other and to us. Think of sensors on equipment feeding data to systems that help humans make better decisions (or sometimes make decisions automatically).
I remember walking through a paper mill in Wisconsin back in 2018 where maintenance crews still relied on the sound of machines to detect problems (“That bearing doesn’t sound right”). Today, that same facility has sensors monitoring temperature, vibration, and dozens of other parameters, sending alerts before anyone’s ear could catch an issue. That’s IIoT in action.
The Trends That Are Actually Making an Impact
1. Predictive Maintenance That Finally Delivers
For years, we heard about predictive maintenance without seeing much real-world impact. That’s changed dramatically. At a automotive parts manufacturer I visited in Michigan last quarter, they’ve slashed unplanned downtime by 37% using vibration sensors and machine learning algorithms that spot anomalies.
Their maintenance manager Tom told me, “We were skeptical at first—we’ve been fixing these machines for 20 years and didn’t think an algorithm could tell us anything new.” Six months in, Tom’s team has become believers. They recently caught a $50,000 bearing failure two weeks before it would have shut down their main production line.
The market’s growing fast—probably around $11 billion now and heading toward $45-50 billion in a few years—but what matters isn’t market size but practical results. Companies I work with are seeing 20-30% maintenance cost reductions, and that goes straight to the bottom line.
2. Digital Twins That Maintenance Crews Actually Use
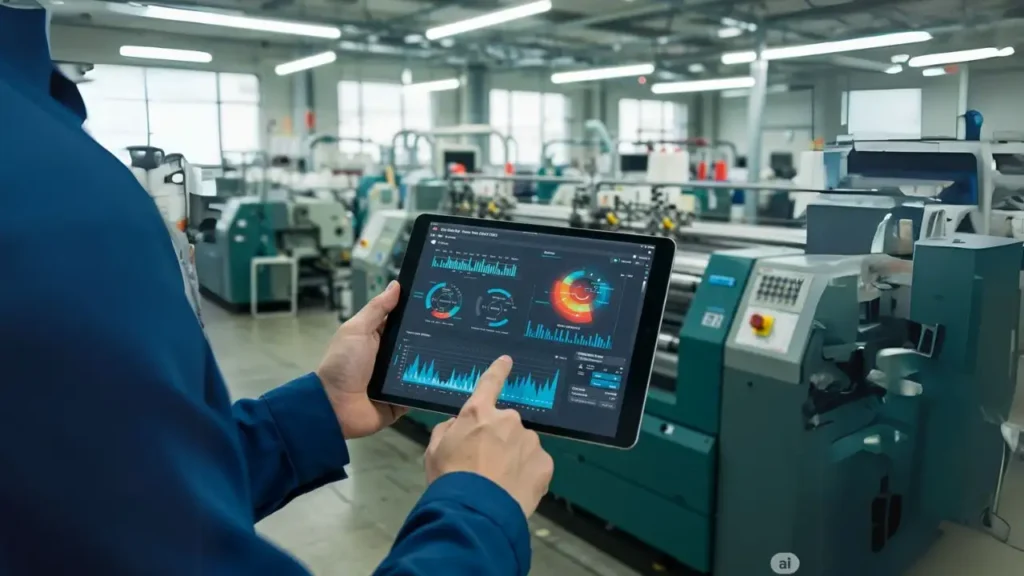
I’ve lost count of how many beautiful digital twin demos I’ve seen at conferences that never made it to the shop floor. What’s changed recently is usability. A textile manufacturer in North Carolina implemented digital twins last year with an interface simple enough that their longtime maintenance staff—some of whom still prefer flip phones—actually embraced it.
“We made a breakthrough when we stopped trying to make it look like a video game and started designing it for the people who’d use it daily,” their operations director explained to me over coffee. Their system lets workers visualize heat distribution across dyeing equipment, something previously impossible to see. They’ve cut setup time between batches by 22 minutes on average.
Buy hot sale replica Breitling watches here online : Bentley Avenger Chronomat B01 Navitimer Certifie Transocean Superocean and more
3. Edge Computing That Solves Real Problems
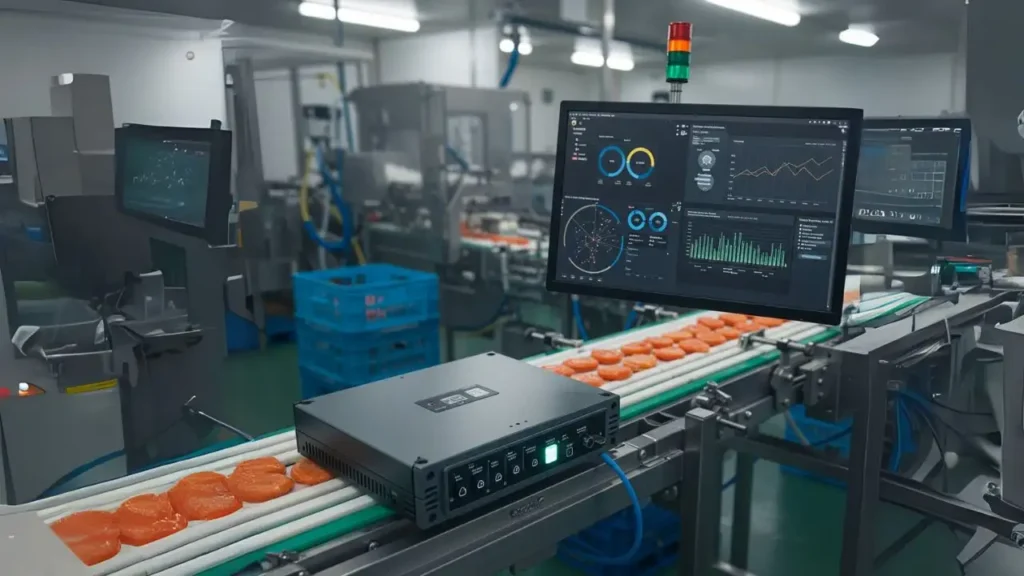
The term “edge computing” makes most factory managers’ eyes glaze over, but the practical applications are solving headaches that have plagued manufacturing for years. Consider a food processing plant I consulted with in Oregon—their quality inspection system generated so much data that their network couldn’t keep up, causing delays and missed defects.
Moving processing power directly to the production line solved their problem overnight. As their IT director put it, “We stopped trying to send mountains of data to the server room and started making decisions right where the product is.” Their defect detection rate improved by 23%, and network congestion disappeared entirely.
This isn’t just about fancy tech—it’s about making systems work in environments where milliseconds and reliability matter.
4. 5G That’s More Than Just Hype

I’ll be honest—I rolled my eyes at early 5G manufacturing presentations. The reality never matched the promise. But I recently walked through a heavy equipment factory in Illinois that’s actually delivering on the potential.
Their facility uses 5G to connect over 400 tools and sensors that previously required wired connections. “The flexibility has transformed how we configure our lines,” explained their operations lead. “We used to spend weeks running new cables when we needed to reconfigure. Now we can move equipment in hours.”
What impressed me wasn’t the technology itself but how it solved a specific pain point—rigid production lines that couldn’t adapt to changing product mixes.
5. Cybersecurity That Manufacturing Actually Implements
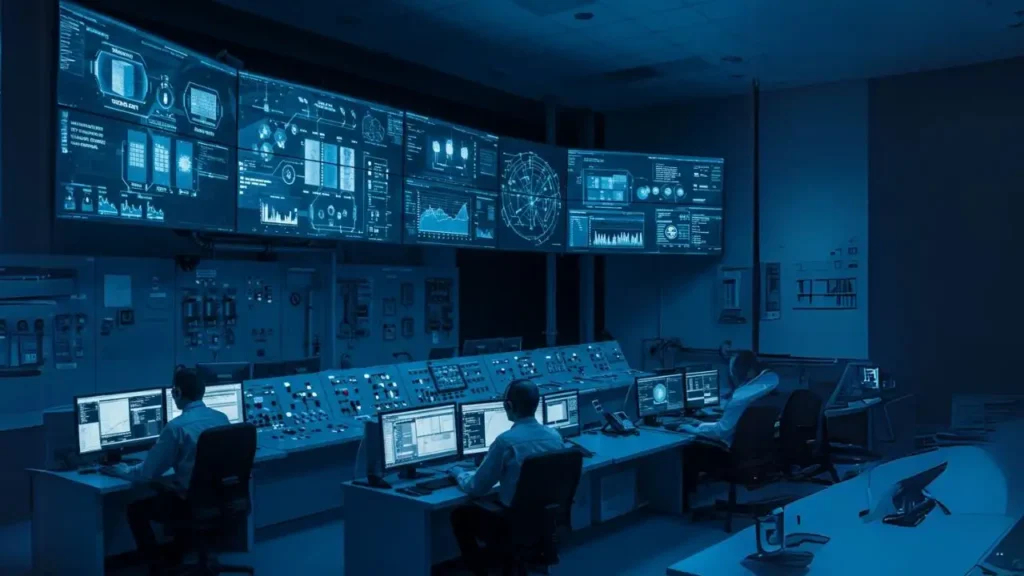
Here’s an uncomfortable truth: manufacturing cybersecurity has been abysmal. I’ve walked into multi-million dollar facilities where network passwords were taped to monitors. That’s changing—not because factories suddenly care about IT best practices, but because they’ve had no choice after several high-profile ransomware attacks shut down production.
A pharmaceutical packaging company I work with recently implemented a zero-trust architecture after a competitor lost three days of production to ransomware. Their approach wasn’t built by cybersecurity theorists but pragmatic engineers who understood both security and operational requirements.
“We designed it so production can never be held hostage,” their security lead told me. Their system isolates each production cell so a compromise in one area can’t spread—a practical approach that doesn’t sacrifice efficiency.
6. Robots That Workers Welcome (Mostly)
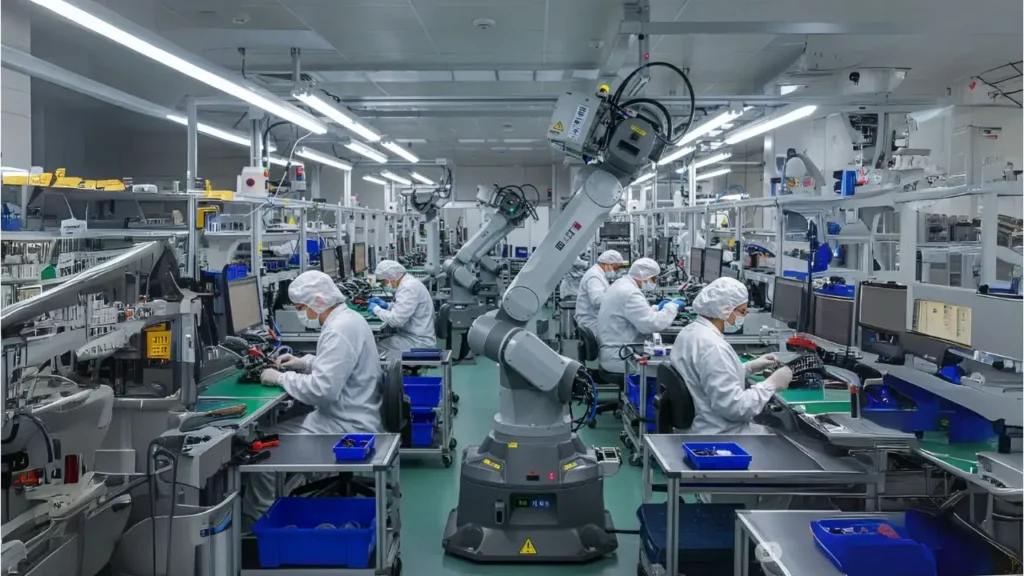
The narrative around industrial robots has been dominated by fear of job losses. What I’ve observed on factory floors tells a different story. At an electronics assembly plant in Arizona, collaborative robots now handle the mind-numbing repetitive tasks that caused high turnover and repetitive strain injuries.
“Our veteran assemblers hated these tasks anyway,” the plant manager shared. “Now they supervise multiple stations and troubleshoot problems—more engaging work that leverages their experience.” Their retention has improved 40% since implementing these systems.
That said, not everyone adapts easily. The most successful implementations I’ve seen invest heavily in training and involve floor workers in the deployment planning from day one.
7. Interfaces That Don’t Require an Engineering Degree
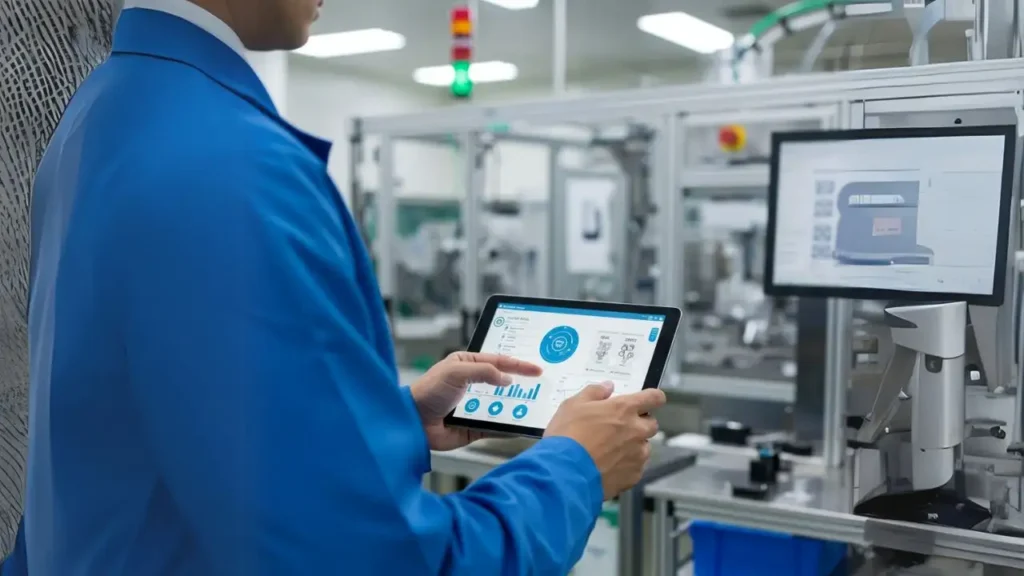
The clunky HMIs (Human-Machine Interfaces) that have dominated factories are finally being replaced with systems that make sense to actual humans. I recently observed production at a medical device manufacturer where operators interact with equipment using voice commands and simplified tablet interfaces.
“We designed it by following operators around for weeks and listening to their frustrations,” their technology director explained. The result? Training time for new operators dropped from three weeks to four days, and error rates have declined by 26%.
The best part is seeing veteran operators who once avoided computer systems now enthusiastically showing others how to use these more intuitive interfaces.
8. Sustainability That Pays for Itself
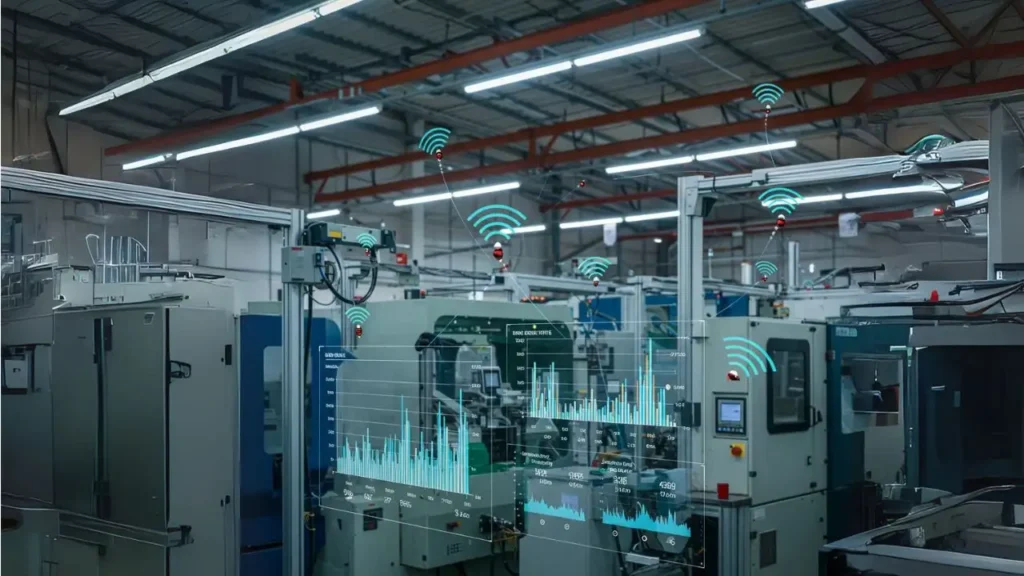
The manufacturing facilities making the biggest sustainability strides aren’t doing it just for environmental reasons—they’ve found the sweet spot where green initiatives drive cost savings. A plastics manufacturer I visited in Texas installed IoT sensors throughout their facility to monitor energy consumption down to the machine level.
“We discovered our chillers were running at full capacity overnight when nothing required cooling,” their engineering manager told me. Simple adjustments from these insights cut their energy bill by 17%, paying for the entire system in 11 months.
What works isn’t grand sustainability initiatives but practical, targeted improvements driven by data that was previously invisible.
9. Cloud Systems That Don’t Terrify Operations Teams
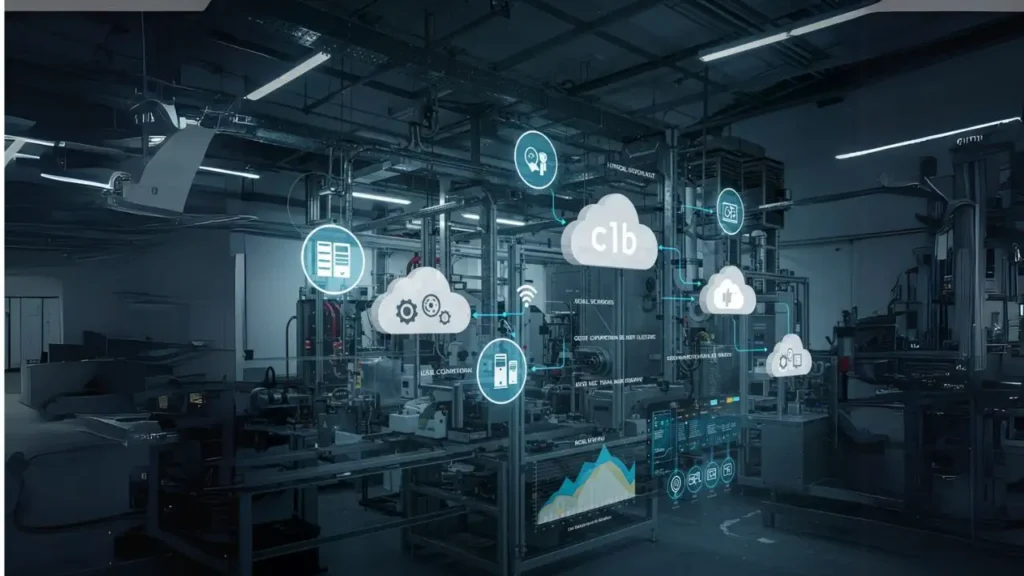
Five years ago, suggesting cloud-based systems to manufacturing operations teams would get you laughed out of the room. “We can’t have production depending on an internet connection!” was the common refrain. The shift I’ve witnessed comes from hybrid architectures that provide cloud benefits without the perceived risks.
A batch processing facility in New Jersey moved to a cloud-native system last year, but with critical control functions running locally. “We get the best of both worlds,” their CTO explained during my visit. “Data analysis and visibility across facilities, but production never stops even if connectivity does.” Their approach has given them new capabilities while respecting the valid concerns of operations teams.
10. Supply Chain Visibility That Actually Works
Factory dashboard showing real-time supply chain tracking and material flow.
Perhaps nothing exposed manufacturing’s weaknesses like the supply chain chaos of recent years. A furniture manufacturer I consulted with last month described their previous inventory management as “basically educated guessing.” Now, they’ve integrated IoT tracking across their supply chain that gives them visibility from raw materials to finished delivery.
“We can see exactly where the bottlenecks are—whether it’s in our facility, at suppliers, or in logistics,” their supply chain manager demonstrated. When a foam supplier recently had production issues, they identified the problem three days earlier than they would have previously, allowing them to adjust production schedules and notify customers proactively.
What makes their system work isn’t just technology, but how they’ve built collaborative relationships with suppliers who share data through standardized systems.
The Real-World Impact
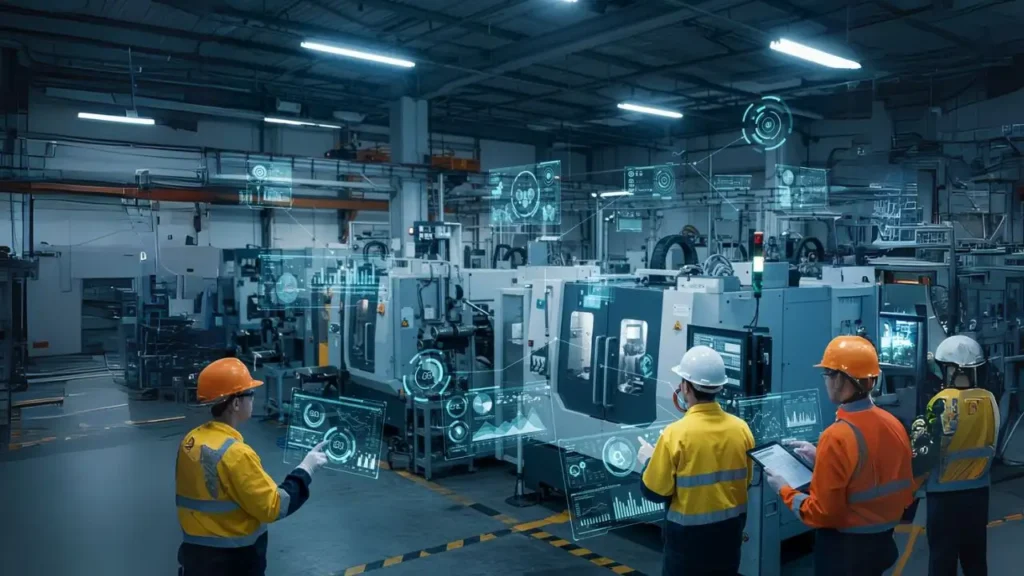
Beyond the technologies themselves, what strikes me in my factory visits is the cultural shift. Manufacturing has traditionally been resistant to change—for good reason, when your priority is consistent output. The most successful digitalization efforts I’ve seen haven’t focused on technology first, but on the people who’ll use it.
A plant manager in Detroit summed it up well: “The tech is the easy part. Getting people to change how they’ve worked for 30 years is the real challenge.”
The most successful IIoT implementations start small, demonstrate clear value, and expand based on shop-floor feedback. They’re led by people who understand both the technology and the realities of production environments.
As for what’s next? I’m watching the integration of these separate technologies into cohesive systems—where predictive maintenance informs production scheduling, which adjusts supply chain planning automatically. The factories moving in this direction aren’t just more efficient; they’re more responsive to both problems and opportunities.
What IIoT trends are you seeing in your industry? I’d love to hear your experiences in the comments below.
Leave a Reply